Rebuilding Teatro La Fenice from its ashes – awe inspiring, behind the scenes solutions
Gran Teatro La Fenice – The Phoenix – is the iconic opera house of Venice, Italy. It is one of the most famous and renowned theatres in Italian history, but unfortunately, it burnt to the ground on 29 January 1996, despite 10 hours of heroic efforts by firefighters on land, in the air, and on water. Nothing remained but a few charred walls…
The city of Venice has decided to restore the theatre to its former glory, as its name suggests.
The phoenix is a beautiful mythological bird that builds a nest of cinnamon twigs at the end of its life, sets it on fire, and burns to ashes with it. From the ashes, a new young phoenix is born.
The world renowned acoustics of La Fenice was most likely based on an extraordinary equilibrium. In fact there were some jutting parts at the top of the theater just below the gallery. And this was the La Fenice that was destroyed.
Guiseppe Paranello – University di Trieste
PROFESSIONALS AS ONE BIG ORCHESTRA
Through our teacher Mr Naldo Busato, Venetian Building Restoration Master, we had the opportunity to gain insight into what it took to revive this architectural masterpiece.
Witness the collaboration that harnessed the skills of the greatest masters to recreate the vision of the original creators. The team faced an extraordinary, almost impossible challenge: resurrecting the theatre, with its paintings, sculptures, world-class acoustics, and luxurious wall decorations, from photographs and documents from the archives.
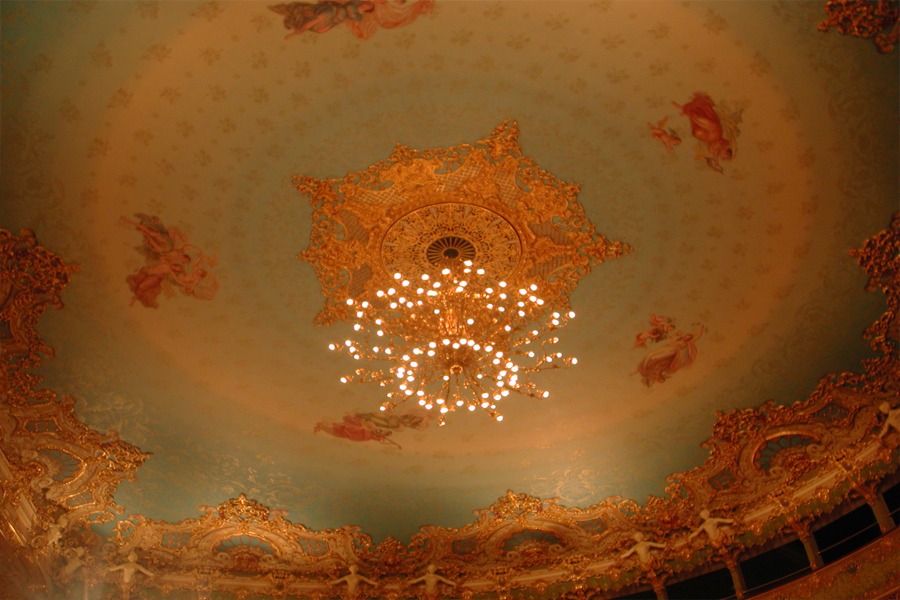
The soul of opera: acoustics
ARCHITECTURE - HISTORIC BUILDING RESTORATION
The main difficulty was that the entire roof, including the cupola — the most important architectural element contributing to the world-class acoustics of the theatre — burnt down and collapsed. Unfortunately it was not possible to examine the solutions of the original structure; only photographs and previously recorded internal dimensions supported the the rebuild.
The task of rebuilding it was given to our tutor, Mr Naldo Busato, the last living member of the Venetian building restoration guild, who was trusted to have the experience and knowledge to rebuild this important element of the opera using traditional building materials and techniques. The project started in his workshop where a section of the cupola was built and tested.
Imagine the building as a beautifully decorated wooden box within the outer walls, creating a unique visual and, above all, acoustic effect. It was known that a hollow place would be needed under the roof, followed by a lightweight wooden parabola serving as a sound reflector, on which the ornate lime plaster ceiling could be built.
The construction of the timber structure in the workshop was followed by the application of the traditional Venetian Cocciopesto plaster.
The recipe was tailored for this specific purpose, ensuring good adherence to timber and increased flexibility to prevent cracking of the ornate painted ceiling, as the timber structure and the entire building were known to move slightly.
As shown in the photos, the plaster was carefully pressed through the gaps of the frame, and a layer of plaster was applied to the backside of the timber to ensure long-term stability.
WOULD YOU LIKE TO KNOW MORE?
CARPENTRY & FURNISHINGS
In the auditorium, all the boxes were crafted from well-seasoned larch wood sourced from the same woods that once provided for the original theatre. The work of a Milanese furniture maker deserves praise, as they meticulously recreated both the boxes and every piece of interior furniture.
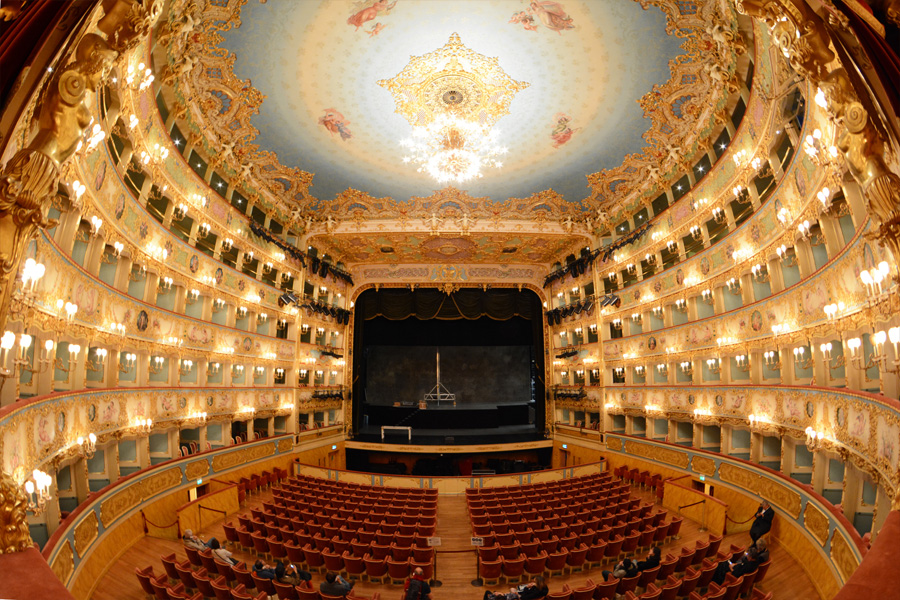
INTERIOR: TRIBUTE TO THE ARTISTS
SCULPTURES AND RELIEFS
They are the masterpieces of Guerrino Lovato, a model maker from a Venetian mask studio, who successfully undertook the task of creating precise replicas of 18th-century sculptural forms. He achieved this by studying photographs of the originals, despite the distortion in the images.
PAINTINGS AND MURALS
Authentic paintings in the lobby and the Royal Box pay tribute to the work of Alma Ortolan and her team. The notes of the Meduna brothers (the architects who rebuilt the theatre in 1837), photographic archives, and laser measurements of the ruins helped create the most accurate computer drawings guiding the artists.

the dazzling ‘marble’ lobby
ARCHITECTURE ONCE AGAIN
HISTORIC BUILDING RESTORATION - BEHIND THE SCENES
Contrary to popular belief, the majestic marble patterns in the lobby were not entirely marble. A lighter, breathable material that can handle humidity well was required, so the Venetian masters used marble-effect lime plaster, when this current design first appeared in the lobby in 1837.
The material is known as Marmorino Veneziano, which translates to ‘little marble’ in Italian. It consists of a mixture of lime putty and marble dust. This classic 15th-century decorative finish was developed during the Renaissance in Venice, possibly as a lighter substitute for marble. Today, it remains one of the most elegant and high-quality decorative lime plasters sought after by architects and interior designers worldwide.
In 2004, the recreation of the luxurious interior plastering began in the workshop of MGN. Samples of the original marble patterns and colours were meticulously recreated based on available photographs. They were flawless in every detail, and the application of the Cocciopesto base with the Stucco Marmorino finish on top commenced in the theater.
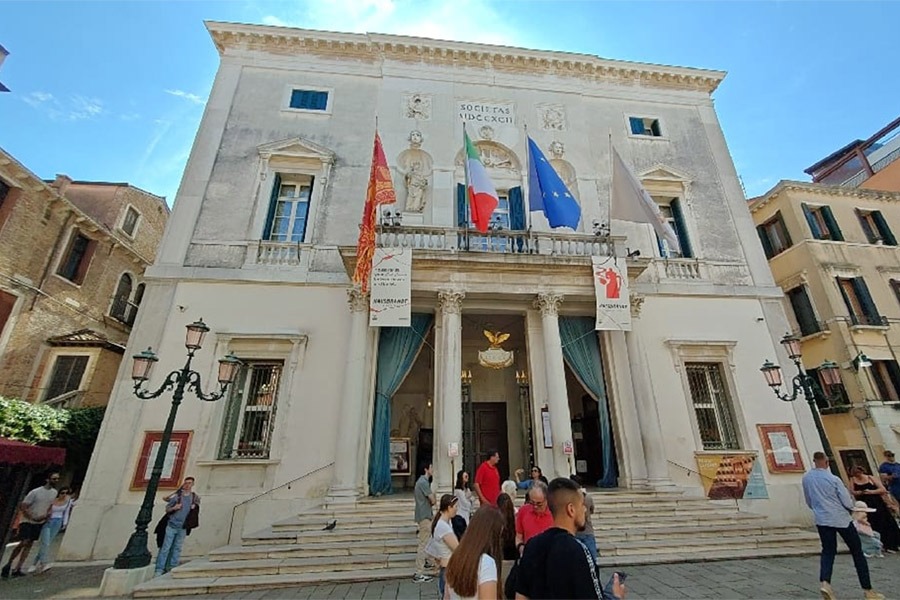
the Exterior
The façade of the building underwent thorough cleaning and stone work restoration.
The side walls have been lime rendered using Cocciopesto, a highly breathable and flexible lime render, following Venetian traditions.
Beyond tradition, Cocciopesto plasters and renders are used because they almost become one with the original brick masonry. Walls are constructed using lime and brick, and Cocciopesto plasters are also made from a mix of lime and crushed bricks. As a result, the plaster is as flexible as the building, with the same thermal expansion, porosity, and breathability.
It simply is the best plaster for the building, and the Venetians knew it.
And so it was that La Fenice – The Phoenix - was resurrected as a tribute to Venice's better days
It is always a deeply emotional experience to sing Violetta in a newly reborn theatre. It is liket the story of Violetta who dies who lives, is burnt by life and is reborn again, through love. You need a lot of love to rebuild a theatre. Music is love.
Patrizia Ciofi – Opera Singer
ARE YOU STRUGGLING WITH A CHALLENGING PROJECT?
We consult you free of charge
LEARN MORE ABUT THE ABOVE MENTIONED PRODUCTS
Rebuilding Teatro La Fenice from its ashes – awe inspiring, behind the scenes solutions Read More »